CASE STUDY
MOLDED PULP VS. FOAM

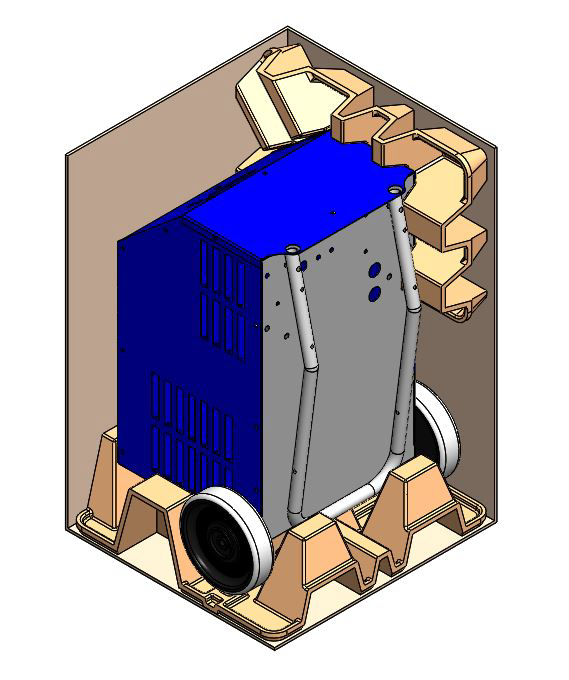
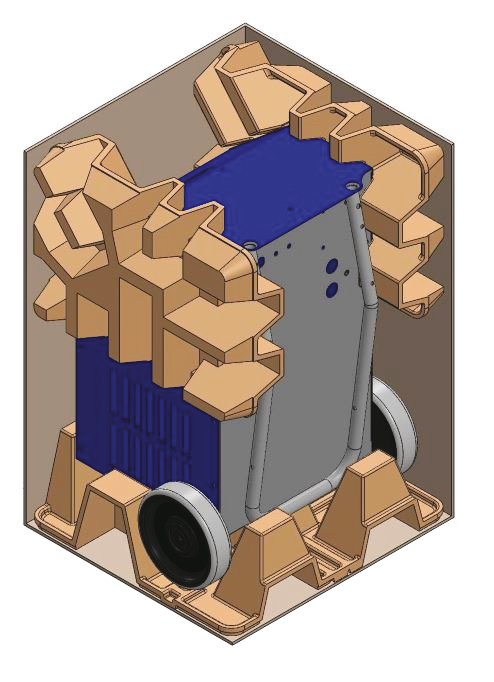
Application
50 Pound Mobile Charging Station
Previous Material
Foam
THE CHALLENGE
Due to the size of the foam packaging, the customer was packing their product in large boxes, measuring 29.75” in height. The size of the boxes drove increased storage and shipping costs, as the boxes took up significant space in the warehouse and fewer units could be shipped on a truck. Moreover, the customer was concerned about the environmental effects foam has on the planet, being a foam material that is rarely recycled or decomposed. Finally, the customer was looking to reduce overall packaging costs.THE SOLUTION
Keiding, Inc. created a three part molded pulp solution with a compact design, aimed at maximizing protection while reducing the packaging footprint, and like all molded pulp is environmentally friendly.THE RESULT
The customer has saved $75k annually since switching to Keiding’s molded pulp packaging solution. Due to the innovative pulp design, the customer was able to reduce the height of their boxes from 29.75” to 24.75”, a -16.7% reduction in overall box volume. This led to a $30k savings in warehouse and shipping costs, for more units could be shipped on a truck than before. A further $45k was saved simply due to the lower costs of Keiding’s molded pulp product. In addition to the monetary savings molded pulp provided, the customer is happy knowing their packaging is environmentally friendly, both recycled and recyclable.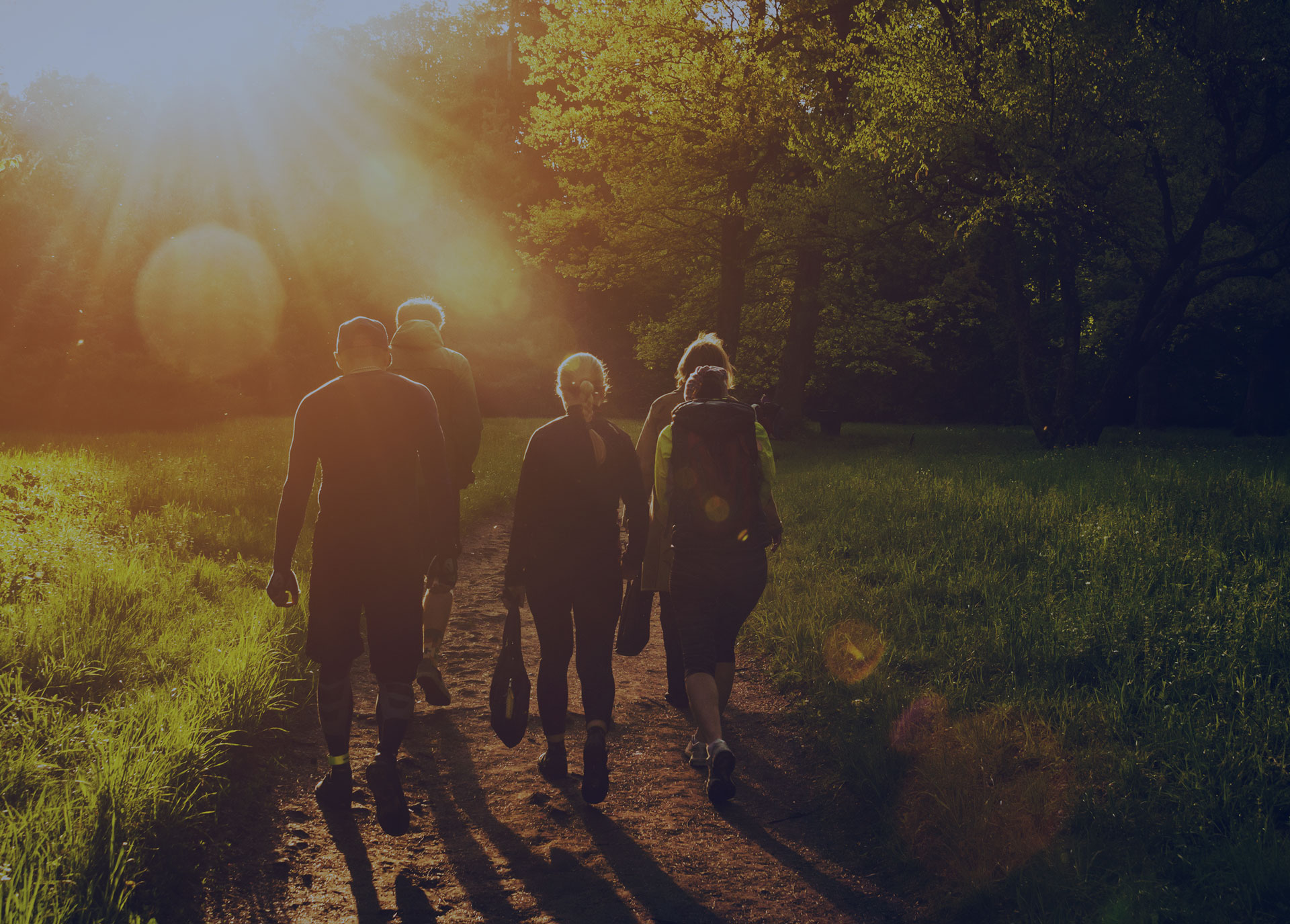
We Think INSIDE the Box
Is your product over 10 pounds per individual piece? Are you looking for support, blocking or bracing package applications? If so, our Type 1 heavy-wall molded pulp may be the perfect solution you’re searching for. Complete the short form and a packaging specialist will review your product!