CASE STUDY
MOLDED PULP VS. HEXACOMB
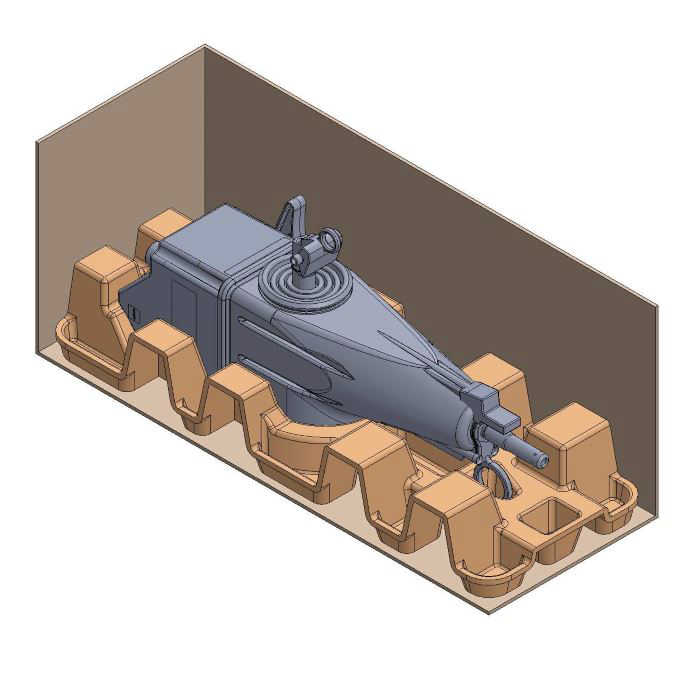
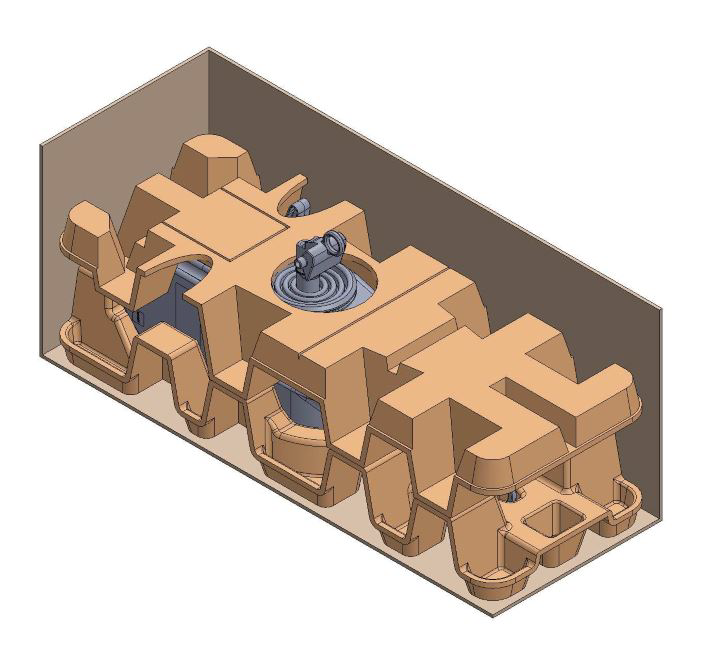
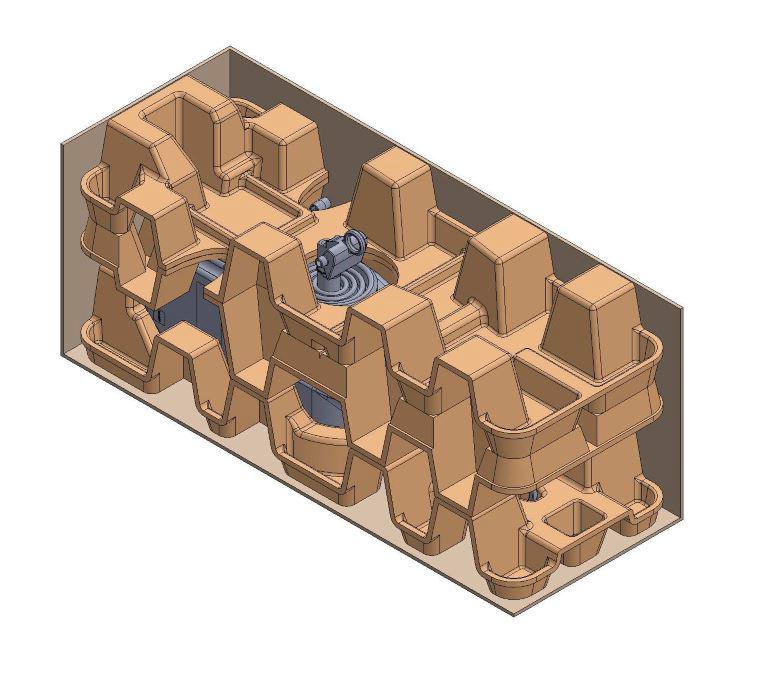
Application
Industrial Electronic Component
Previous Material
Five Part (SKU) Corrugated Hexacomb
THE CHALLENGE
The size and complexity of the customer’s previous five-part Hexacomb solution was driving increased storage, shipping and production costs. A significant percentage of their warehouse space was consumed by the Hexacomb packaging, which also meant truck-load capacity was inefficient; they were bringing in five truckloads of packaging per week. In addition, too much time was being spent packing the customer’s 40lb electronic component on the production line having to piece together five separate parts to form one packaging solution.THE SOLUTION
Keiding Inc created a molded pulp solution with a sleek, compact design that is strong in all directions, reducing the number of packaging SKUs from five down to two, both with warehouse saving nesting capabilities.THE RESULT
The customer decreased annual shipping and storage costs by $100k since switching to Keiding’s molded pulp packaging solution. Due to fewer packing parts and nesting capabilities, they have experienced warehouse space savings, thus increasing their finished good storage and creating value for their customers in the form of a quick turnaround. Truckload capacity has increased by +400%, reducing their weekly packaging truck-loads from five down to one. Finally, time spent packing their product has decreased dramatically.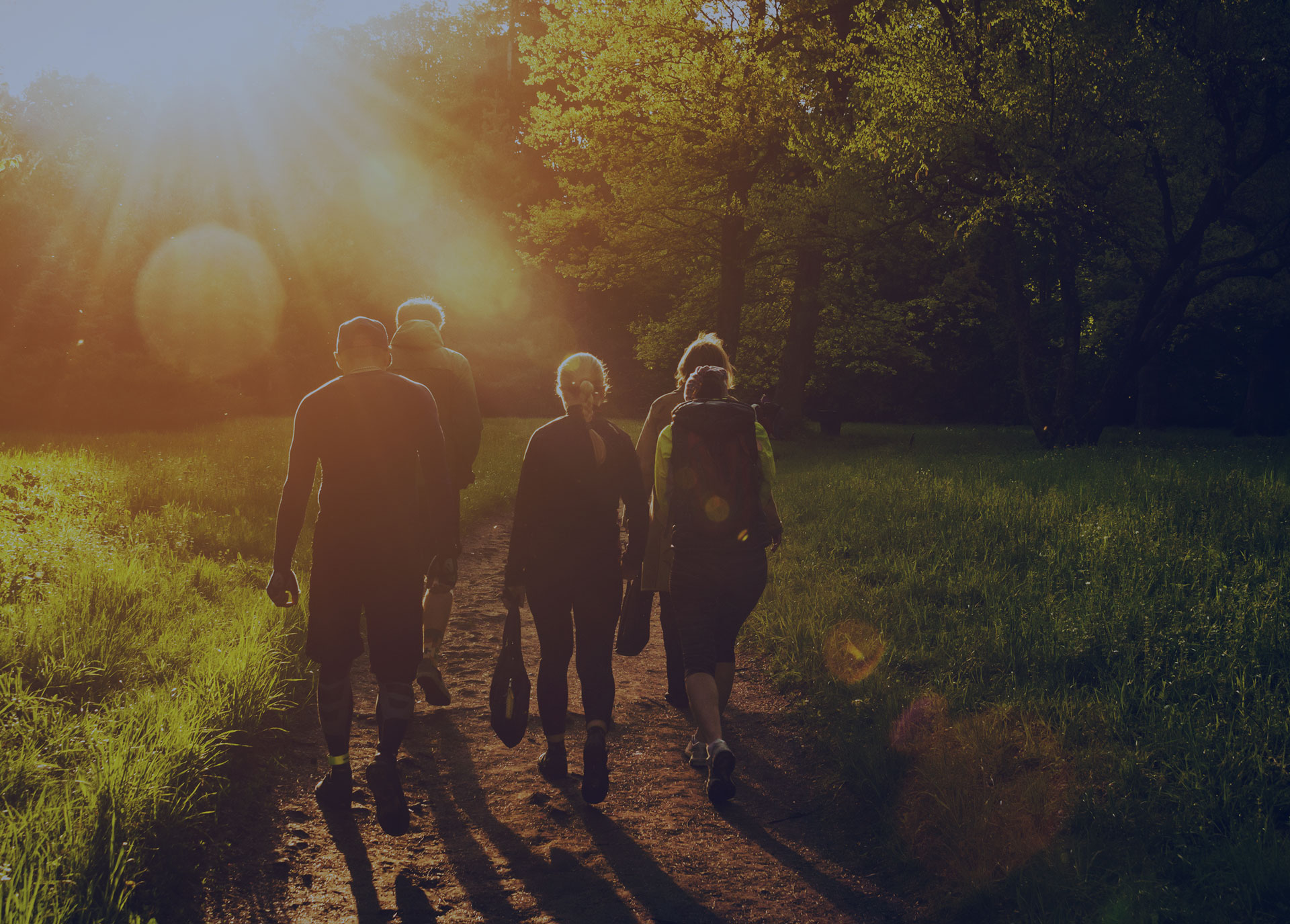
We Think INSIDE the Box
Is your product over 10 pounds per individual piece?
Are you looking for support, blocking or bracing package applications?
If so, our Type 1 heavy-wall molded pulp may be the perfect solution you’re searching for. Complete the short form and a packaging specialist will review your product!