How Molded Pulp Stacks Up Against the Competition
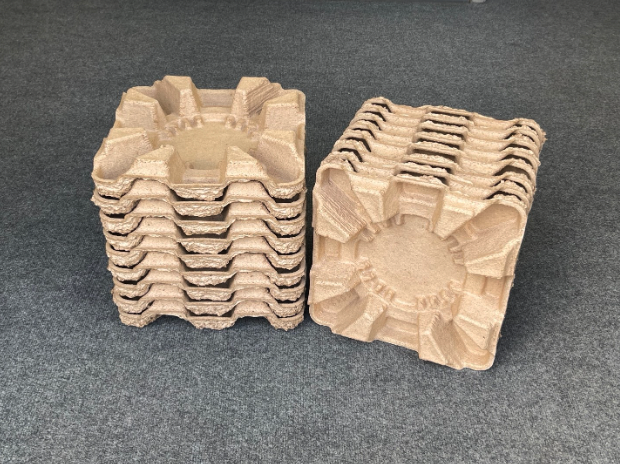
Companies across the world innovate daily on their products and services to become increasingly eco-friendly. With service-based businesses, this often means fewer corporate flights, more digital documents, and environmentally friendly operating procedures. For businesses that produce goods, the challenge lies in product development and logistics. As consumers also become increasingly green, it’s important that products are biodegradable or recyclable and made from high-quality recycled materials whenever possible.
Often, the eco-friendly ingredient of choice ends up being in the paper family. Paper fibers are biodegradable, recyclable, and versatile, making paper a great component in creating environmentally friendly goods (and in our case, packaging at scale).
Molded Pulp Packaging
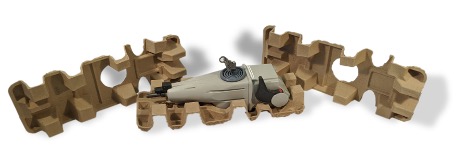
Molded pulp packaging is made from a mixture of water and natural fibers that are vacuum formed into a desired shape. The materials used and the dimensional shape will determine the coloring and strength of the packaging.
Originally used for eggs, molded pulp packaging has expanded into other industries offering a new, slick feel. The healthcare industry uses molded pulp for kidney trays, preserving the sterile environment of a hospital, Apple uses it for safely transporting electronics, while Insinkerator promotes the reduction in food and packaging waste that impacts landfill sites and the wider environment.
Additionally, molded pulp packaging helps fight the global environmental crisis by using waste byproducts as its composition. Plastic is manufactured at a rate that is twice what it was 20 years ago, and only 9 percent of that is successfully recycled. Molded pulp provides innovative packaging solutions to reduce plastic waste.
Keiding understands the hesitation of switching from traditional packaging material to molded pulp packaging, so let’s distinguish between this material and older packaging alternatives.
Hexacomb vs Molded Pulp
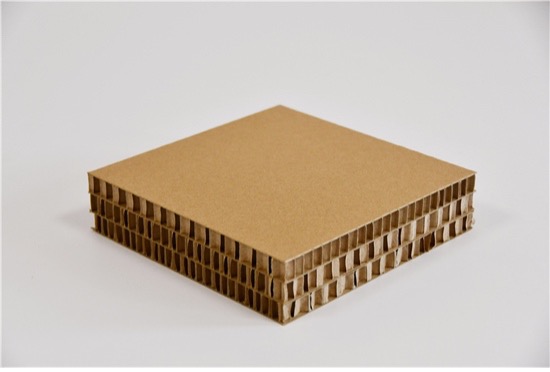
Hexacomb, also known as “honeycomb”, provides durable cushioning for products such as furniture, glass, and signage displays. As it’s primarily made of paper, like molded pulp packaging, Hexacomb is eco-friendly and sustainable for our environment. Hexacomb is primarily formed by uniting individual bands of Kraft paper to build consistent loops of hexagonal cells. Hexacomb is lightweight and prevents the disentangling of products during transportation.
However, Hexacomb lacks versatility and is less cost effective. As molded pulp packaging does not require much assembly, labor costs also are significantly reduced. While molded pulp packaging can be molded to form protection for any product on the market, Hexacomb is strictly for holding a “box” shape, not able to meet the needs of many products.
Bubble Wrap vs Molded Pulp
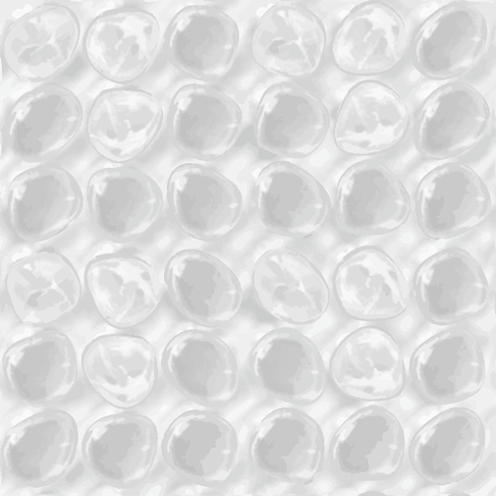
Bubble wrap is not only an interactive distraction for little ones, but it has had a successful track record of preventing shock to encased products. Bubble wrap is composed of polyethylene resin formed into tiny beads. The beads are melted to create a thin film. With its bubble cushions, bubble wrap is primarily used for very fragile products.
However, bubble wrap is extremely difficult to recycle. It is not biodegradable and is a huge storage hassle, slowly filling up landfills. Additionally, the combination of the plentiful oxygen bubbles presents a foundation for a flammable hazard. The last thing we want to see is your products catch on fire, so other packaging alternatives, like molded pulp, are a smarter option.
Styrofoam vs Molded Pulp
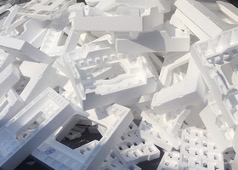
Invented in 1944 by Ray McIntire, Styrofoam has been one of the initial and longest packaging solutions in the industry. Styrofoam’s composition is made from styrene that is converted into polystyrene through polymerization, and then followed by the addition of a hydrofluorocarbon activator. After being released, this mixture contracts under stress until it takes the shape of a foam board.
Styrofoam works well with products of various temperatures and thus is primarily used in the food industry. However, Styrofoam is a big environmental risk. When exposed to light, Styrofoam releases air pollutants that could deplete the ozone layer. It is also found in landfills, and animals often mistake it for food. Molded pulp can be recycled and revived for all products without hurting the environment or living creatures.
Keiding’s Packaging Solutions
Companies looking for industrial, consumer, or commercial product packaging solutions that are durable and environmentally friendly should start with Keiding. We customize based to your needs and deliver at scale. Plus, if your product is over 10 pounds per individual piece, we offer a heavy-wall molded pulp for extra support.
With nearly 85 years of experience, Keiding has the credentials to protect your products.
Get Started
Contact us to find out how we can help you with environmentally sustainable packaging or to learn more about molded pulp solutions!